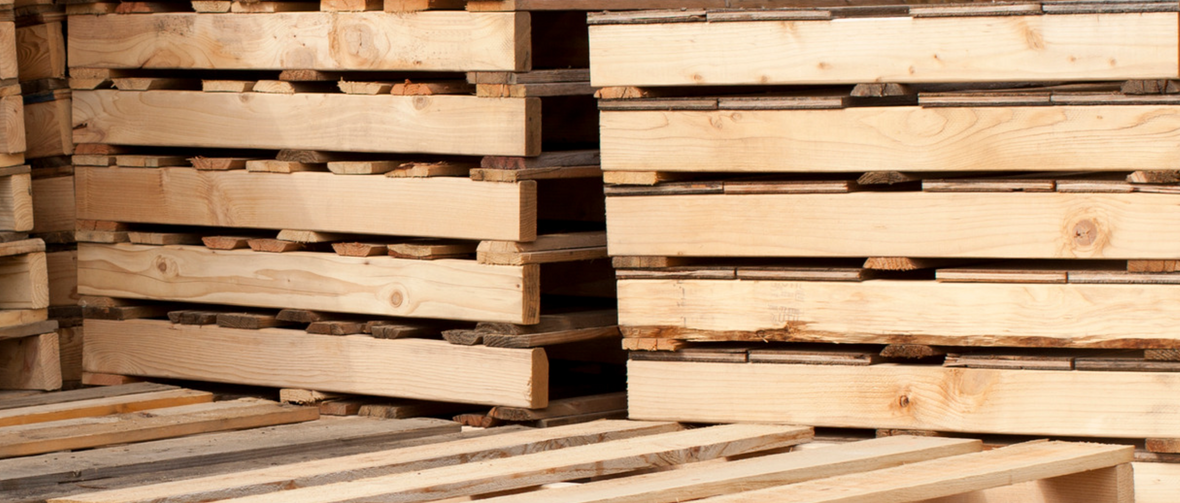
Shipping Pallets: What to do, and What to Avoid
Ensuring safe and secure transport of goods is part of running an effective business.
Shipping pallets is a common practice in the food industry, where proper packaging is crucial to maintaining the quality and safety of the products being transported. Whether you're shipping temperature-controlled products or dry goods, ensuring that pallets are wrapped and packed securely is essential to prevent damage during transit.
This blog will walk you through the process of properly packing and wrapping a pallet for shipment, including tips on how to avoid common mistakes, how to choose the right shipping carrier, and how to inspect the truck to ensure it is safe for transporting food products.
1. Packing Boxes Correctly: Building a Sturdy Foundation
Before wrapping the pallet, it’s important to make sure that the boxes are packed properly. A well-packed pallet begins with sturdy, well-arranged boxes. Here's how to do it right:
- Choose the Right Box Sizes: Use boxes that are appropriate for the size of your products and stack them evenly. Avoid using boxes that are too large or too small, as this can cause instability during transport.
- Heavy Boxes on the Bottom: Always stack the heaviest boxes at the bottom of the pallet. This creates a stable foundation and helps prevent the pallet from toppling over. Lighter boxes should be placed on top to maintain balance.
- No Overhanging Boxes: Ensure that no boxes are hanging over the edges of the pallet. Overhanging boxes can easily be damaged during transport and can cause the pallet to become unstable.
- Use Interlocking Patterns: Stack the boxes in a brick or interlocking pattern, so the weight is distributed evenly across the pallet. This helps prevent shifting during transit and adds extra stability.
2. Preparing the Pallet: Proper Height and Load Limits
The height of the pallet is a key factor in ensuring that it remains stable during shipping. Generally, a pallet should not be taller than 60 to 72 inches (about 5 to 6 feet). Taller pallets are more prone to tipping over, especially if they are not packed securely.
Before wrapping the pallet, check that the total weight of the goods is within the capacity of the pallet itself. The most common pallets are designed to hold up to 2,200 pounds (1,000 kg), but this may vary based on the type of pallet and the goods being shipped. Make sure you are not exceeding the load limits, as overloading can result in damage to the pallet and the products during transit.
3. Wrapping the Pallet: Tying and Tightening the Plastic Wrap
Proper wrapping ensures that the boxes stay in place and that the pallet remains stable throughout transport. Here’s a step-by-step guide on how to do it:
- Tie the Wrap to the Pallet: Start by tying the plastic wrap (also known as stretch film) securely to the base of the pallet. This prevents the wrap from shifting as you begin the process. To tie the wrap, pull out a long piece of wrap and tuck it between two slats on the bottom of the pallet. Twist it slightly to create a firm starting point.
- Pull the Wrap Tight: As you begin wrapping, pull the stretch film tightly to eliminate slack. Keeping the wrap tight ensures that the boxes stay securely in place and that the pallet maintains its integrity during shipping.
- Wrap the Pallet 3-5 Times Around the Base: Begin wrapping at the base of the pallet, securing the bottom portion by circling it three to five times with the wrap. This ensures that the boxes are tied to the pallet itself and that the load remains stable. Once the base is secure, move upward, wrapping the rest of the pallet.
- Continue Wrapping Upward: After securing the base, continue wrapping up the pallet, making sure to overlap each layer by about 50%. This overlapping ensures there are no gaps where boxes could shift or the wrap could tear.
- Secure the Top of the Pallet: Once you reach the top, wrap it an additional two to three times to make sure the entire load is covered and secured. If you’re shipping temperature-sensitive products, consider using thermal wrap or an insulated cover at the top to maintain the proper temperature.
4. How Many Times to Wrap the Pallet
The number of times you should wrap the pallet depends on the weight and size of the load. For light to medium loads, wrapping the pallet 3-5 times is generally sufficient. Heavier or taller loads may require 6-8 wraps for added security. It’s better to err on the side of caution and apply more wraps if you’re unsure, especially if the shipment will encounter long distances or rough handling.
5. Choosing the Right Shipping Carrier
When shipping pallets, it’s important to choose a carrier that understands the specific needs of food products, especially if they are temperature-sensitive. Here's what to consider:
- Temperature-Controlled Goods: If your products require refrigeration or freezing, make sure you choose a carrier with refrigerated trucks or temperature-controlled containers. Look for a carrier with experience handling perishable goods, as they will understand the importance of maintaining strict temperature controls throughout the shipping process.
- Dry Goods: For dry or non-temperature-sensitive goods, a standard carrier may be suitable. However, ensure that the carrier still meets cleanliness and safety standards, as food-grade products require high levels of hygiene to prevent contamination.
- Carrier Reputation: Choose a reputable shipping company that has a proven track record in handling food shipments. Look for carriers with food safety certifications, such as ISO 22000 or SQF.
6. Inspecting the Truck for Food Safety Compliance
Before your pallet is loaded onto the truck, inspect the vehicle to ensure it is suitable for transporting food. Some key areas to check include:
- Cleanliness: The truck should be clean and free from any residue, odors, or contaminants from previous shipments. A dirty truck can introduce bacteria or pests into your food products.
- Temperature Controls: For temperature-sensitive shipments, confirm that the truck’s refrigeration system is functioning correctly and maintaining the required temperature. The driver should have temperature monitoring systems in place and be able to show you that the temperature is within the acceptable range for your goods.
- Seals and Security: Ensure that the truck has secure door seals to prevent dust, debris, or pests from entering the vehicle during transit. Check that the doors close tightly and that there are no visible gaps.
- Pallet Placement: Confirm that the pallets will be loaded properly and secured inside the truck to prevent shifting during transport. The driver should have proper equipment, such as load bars or straps, to secure the pallets and prevent damage.
7. Common Mistakes to Avoid When Wrapping Pallets
To ensure the safe arrival of your shipment, avoid these common mistakes when packing and wrapping pallets:
- Not Using Enough Wrap: Insufficient wrapping can cause the pallet to become unstable during transit. Make sure to apply enough layers of plastic wrap, especially around the base and top of the pallet, to secure the load.
- Loose Wrapping: Wrapping the pallet too loosely allows the boxes to shift, increasing the risk of damage. Always pull the wrap tight as you work your way around the pallet.
- Stacking Boxes Too High: Over-stacking boxes can cause the pallet to become unstable and tip over. Stick to a maximum height of 60 to 72 inches.
- Failing to Secure the Pallet to the Load: Not tying the plastic wrap to the pallet itself means the boxes can shift or slide off the pallet. Always anchor the wrap to the pallet base by starting with multiple wraps around the bottom.
- Choosing the Wrong Carrier: Using a shipping carrier that isn’t equipped to handle food products, especially temperature-sensitive items, can lead to spoiled goods or contamination. Always select a carrier with experience and proper safety certifications for food-grade shipments.
- Choosing the Wrong Shipment Route: Sometimes people choose the least expensive shipment option, but this can be a mistake. Less expensive options tend to be slower, and more prone to delays which can ruin a shipment that is perishable. Follow up with your carrier frequently to ensure that the shipment is on time, and for food products that are perishable, ensure that your pallet will be on a truck rather than a train, especially in areas where there is cold weather as icy rails and snow piles can delay shipments up to several weeks.
8. Insuring your Shipment:
Even if you do everything right, sometimes a shipment does not go to plan. Insurance for pallet shipments is an essential safeguard for businesses, especially in the food industry where the value of goods and strict regulatory requirements make losses particularly costly. Shipping insurance covers a wide range of potential issues, including damage, loss, theft, and mishandling during transit. For temperature-controlled shipments, insurance can also protect against spoilage due to equipment failure or delays.
By investing in pallet or container shipment insurance, businesses can mitigate financial risks and avoid significant losses if goods are damaged or lost. This coverage provides peace of mind, allowing companies to recover their costs or replace damaged products, ensuring business continuity and maintaining customer trust. Having insurance in place can also help resolve claims efficiently, reducing the impact on both revenue and supply chain operations.
Wrapping and shipping pallets in the food industry requires careful attention to detail to ensure that your products arrive safely and intact. By properly packing boxes, securing the load with plastic wrap, and selecting the right shipping carrier, you can minimize the risk of damage during transport.
Don’t forget to inspect the truck for food safety compliance and avoid common mistakes such as loose wrapping or over-stacking. By following these steps, you’ll ensure that your pallets are securely packed, wrapped, and shipped, protecting both your products and your business.